
#Aoe membership toolkit full
The last node in a segment (or drop line) detects an open port and sends the message back to the master using Ethernet technology’s full duplex feature. The frame is delayed only by hardware propagation delay times. Each EtherCAT slave device reads the data addressed to it “on the fly”, and inserts its data in the frame as the frame is moving downstream. The EtherCAT master sends a telegram that passes through each node. Conformance and Certification 3.1 Plug Fest Implementing EtherCAT Interfaces 2.1 Masterģ. 1. Features of EtherCAT 1.1 Functional Principleġ.9.1 CAN Application Protocol over EtherCAT (CoE)ġ.9.2 Servo Drive Profile according to IEC 64 over EtherCAT (SoE)ġ.12 EtherCAT, TSN, Industrie 4.0 and IoTĢ.
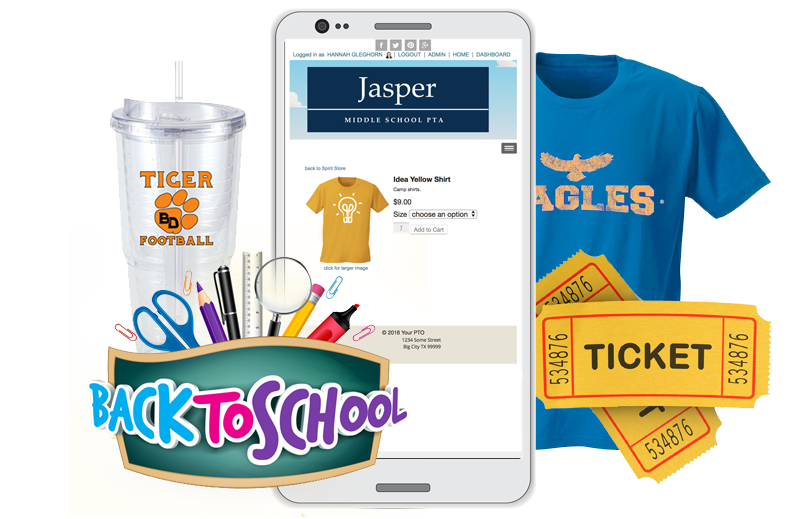
The ETG brings together manufacturers and users, which contribute in technical working groups to the advancement of the EtherCAT technology. The main focus during the development of EtherCAT was on short cycle times (≤ 100 µs), low jitter for accurate synchronization (≤ 1 µs) and low hardware costs.ĮtherCAT was introduced in April 2003, and the EtherCAT Technology Group was founded in November 2003 - Meanwhile ETG has grown into the world’s largest Industrial Ethernet and fieldbus organization. The EtherCAT protocol which is disclosed in the IEC standard IEC61158 is suitable for hard and soft real-time requirements in automation technology, in test and measurement and many other applications.

The following information can also be found the the EtherCAT Brochure, available in various languages.ĮtherCAT is a real-time Industrial Ethernet technology originally developed by Beckhoff Automation. This section provides an in-depth introduction into EtherCAT (Ethernet for Control Automation Technology).
